Tilt Up Panel Construction Toowoomba
Home > Tilt-up Panel Construction
- Versatile Residential, Commercial, & Rural Concreting Services
- More Than 30 Years’ Combined Industry Experience
- Free Quotes Available
Enquiry Form
Tilt Up Panel Construction Experts
Tilt-up panel construction is an extremely time-efficient and cost-effective building technique, ideal for commercial and high-rise buildings.
It involves prefabricating large concrete panels and then lifting them into place and fastening them to a slab. The panels are typically used for walls, columns, and other structural supports.
At McCoy Concreting, we handle all aspects of tilt-up panel construction. Our team can prefabricate concrete slabs directly at your site to minimise transport costs.
Additionally, we can deliver the slab to your site by truck – which is a better option in more urban areas where space is at a premium. We only work with the best equipment and products to ensure all specifications are addressed.
Benefits of Tilt-up Panel Construction
Saves Time Without Compromising Quality
The method is simple: We use pre-fabricated concrete panels, or we even fabricate new panels on-site, then stand them up in place to create the walls of your building. This greatly speeds up construction time on a building, whilst also creating a robust and consistent finish for your construction for enhanced build quality.
Saves You Money
Pouring concrete is a process that takes a significant amount of time, constant attention, and skill - all of which add extra costs to the construction process. By using Tilt-up Panel Construction instead, you can shave a considerable amount of time off the job and save on man-hours. But it's not all a cost-saving exercise, because Tilt-up Panel Construction also improves build quality and durability too!
Reduced Insurance Premiums
Tilt-up panel construction offers a robust finish that lead to reduced insurance premiums because of the inherent fire-resistance and stability of buildings constructed using this technique.
Improved Strength & Durability
Using the pre-fabrication or on-site fabrication method we can ensure that each panel is high quality and standardised, while poured concrete can be of variable quality and thickness if poured incorrectly. Being made of single slabs joined tightly together also improves strength and durability by removing potential faults and points of weakness.
When Should You Consider Tilt-Up Panels
You should consider Tilt-up Panel Construction for buildings that are designed to be as cost-effective and durable as possible, including projects such as commercial and industrial buildings where you need to get as much as you can out of your investment.
Tilt-up Panel Construction is also much more cost-effective than pouring concrete because each panel can be made on-site, which cuts down on transport costs and saves a lot of time, and it also incorporates its own insulation.
It is also easily sealed with a lower number of joints than in other forms of construction, meaning there are fewer points of weakness and it is a tough and airtight method.
Custom Sizes Available For Tilt Up Panels
One of the best things about Tilt-up Panel Construction is that each panel is customisable in a variety of ways, from size and height to the finish used.
This allows you to easily create interesting and customised designs without many of the associated costs in dealing with other methods of construction, including differences in shape and size and other additions like doors and windows.
This is possible because every panel can be custom finished on-site, so you can even make changes as you go.
You can even customise the finish on each panel to have a specific finish or colour, which allows you and the architect to create visually interesting designs without the usual hassle and expense.
Our Tilt Up Panel Construction Process
At McCoy Concreting, we offer comprehensive tilt-up panel construction services. Our primary services are outlined in more detail below.
Prefabrication
We provide prefabricated tilt-up panels for our ease of installation and your general convenience. Prefabrication involves assembling all of the required tilt-up panel components of your construction project either on-site or off-site, which is useful for those projects where construction space is limited.
Delivery
In addition to providing a prefabrication service, here at McCoy Concreting we are able to transport your tilt-up panel order directly to the intended construction site. This minimises hassle and improves the efficiency of your project, as once your order arrives we can simply assemble through to completion.
Installation
Following the delivery of your prefabricated tilt-up panels, our team can construct them on your behalf. This includes the use of specialist, top-of-the-range equipment that can cater exactly to your specifications, leading to a concise and professional job every time.
How Tilt-up Construction Works
Tilt-up construction is a type of construction that works by pre-casting a series of concrete panels. The panels are made either off-site or on-site at the construction location and are made using concrete, rebar and wood forms. These forms are cut to shape before concrete is poured into the forms and left to dry.
If made off-site, the panels are then delivered on-site and tilted up into place, most commonly to form the exterior walls of a building. When being titled into position, the tilt-up panels are placed into foundational footings to ensure stability and sturdiness both during and following construction.
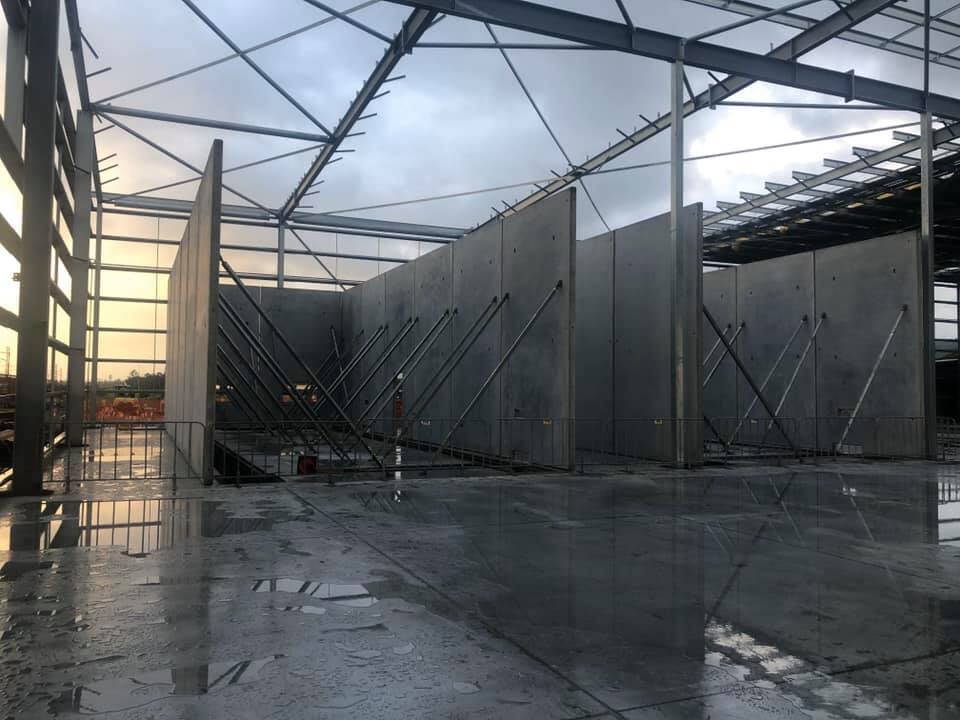
Why Choose McCoy Concreting For Your Tilt-up Panels?
Enhanced Design Flexibility
Tilt-up panel construction offers the great advantage of providing you with enhanced flexibility when it comes to design. Whether your plans include cladding or veneer, tilt-up panels make this possible.
The process of creating the tilt-up panels can also be adjusted using state-of-the-art CAD software to ensure that the panels exactly fit your design plans. This minimises the risk of any unanticipated problems as you can be confident that the panels have been made to exact specifications.
Better Energy Efficiency
Another benefit of opting for tilt-up panels is that reinforced concrete, which the panels tend to be made from, is an excellent insulator. This means that your building will retain heat with great efficiency. Additionally, this thermal retaining quality can be improved through the addition of extra thermal layers such as cladding.
The creation of tile-up panels is also more energy effective than alternative methods such as steel production.
Fewer Workers Needed
Choosing to install tilt-up panels offers another benefit in that it requires fewer workers to install, because of this, manual labour costs will be down and fewer employees are needed on-site, resulting in decreased costs for your construction company.
The erection of tilt-up panels also only typically takes a matter of days, meaning that your construction project will reach completion in less time. This, again, results in lower costs for your company and a higher margin for profits in the future.
Want to learn more?
If You’d Like To Find Out More about our tilt-up panel construction services - or request a free, no-obligation quote – contact us today on 0438 272 749 or online if you'd prefer for us to call you back.
We can take on jobs throughout the Toowoomba region.
Frequently Asked Questions
What are the main advantages of tilt-up construction?
In addition to being cost-effective, the tilt-up method can facilitate a huge range of architectural styles. Additionally, the tilt-up method can significantly reduce construction time while maximising the integrity and durability of the structure.
How thick are the concrete panels used for tilt-up construction?
For commercial walls, the minimal thickness is generally 5½ inches. However, 7¼ inches is the recommended thickness for most builds.
What site conditions can limit or hinder tilt-tray construction?
You should assess whether the site is sufficiently flat, as well as verify that a crane will have easy access to the site. You should also verify if buildings or powerlines in close proximity could impede crane operations.
Is tilt-up panel construction an efficient technique?
Yes, tilt-up is incredibly efficient, especially when compared to older forms of construction that require concrete masonry unit blocks. There are fewer stages of construction with tilt-up and less labour used.
The lower labour costs result in significant savings for construction projects too, making it an excellent return on investment. There are even efficiencies in project timelines because tilt-up is faster than many traditional methods.
What are the stages of a tilt-up project?
Every project is unique and will require different processes for successful completion. With that said, tilt-up projects generally break down into the following stages:
- Site evaluation and pre-planning processes
- Site engineering
- Concrete panel preparation
- Tile panel casting
- Tilting the concrete panels into place
What holds the tilt-up panels in place?
The roof plays a large role in keeping the tilt-up panels secure by acting as a diaphragm that supports the concrete wall at the top. The curb found on the footing supports is also important because it supports the bottom. Panels aren’t connected to each other to give room for movement (such as expansion or compression) without causing cracks in the concrete. The panels are connected to the roof, but only near the top.
Can you insulate a tilt-up wall?
Yes, it’s achieved by insulating the inside with furring systems or on the outside with an exterior insulation finishing system. The best approach is to employ the ‘sandwich’ method, which places insulation between the structural concrete and a non-structural concrete layer. This is usually done while casting the panel before tilting.
The sandwich method works by connecting two concrete layers structurally with the use of an insulation layer. When the panel is put in its final position, the insulation acts as a load-bearing component, which allows the concrete layer to be suspended while it adjusts to temperature changes without the risk of cracks. The only way this works is by having the two panels work independently of one another with the exception of that connection via insulation.
What crane size is required to lift tilt-up panels?
The size of the crane required for this type of work will vary depending on the weight of the panels and the scale of the project. Generally speaking, cranes that can handle three times the weight of a panel are used, but it’s best to let a professional crane company make the decision.